A Look at The Key Components of CNC Plasma Tables
- russ0377
- Feb 25, 2024
- 4 min read

CNC Plasma Tables are like the Swiss Army knives of the metalworking world. They're versatile, reliable, and capable of creating just about anything you can imagine.
But what makes them tick?
What components come together to transform a simple metal sheet into an intricate design?
As your guide to precision cutting, FastCut CNC has had the privilege of turning countless metal sheets into pieces of art and functionality. And today, we're here to let you in on the secrets that lie beneath the hood of these remarkable machines.
Plasma Torch: The Heartbeat of Cutting
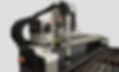
This device is the real heart of the operation—it's where all the magic happens.
The torch is responsible for the 'actual' cutting of the metal and works by sending an electric arc through a gas that is passed through a constricted opening. This process increases the temperature of the gas to the point that it enters a fourth state of matter. Yes, you read that right–a fourth state—plasma.
This super-heated, electrically ionized gas then cuts through your metal, leaving a clean, precise cut in its wake. What's more? Its beauty lies in its versatility—it can cut through a lot of materials including steel, stainless steel, aluminum, brass, and even copper, and it can handle varying thicknesses with ease.
The Brain Behind Precision: CNC Controller
Now, a plasma torch is all well and good, but without direction, it's like a race car driver without a steering wheel.
CNC, stands for Computer Numerical Control, and this technology converts your designs created in computer-aided design (CAD) software into numbers. These are coordinates of a graph that then guides the movement of the cutter.
In other words, it is the mastermind that tells your plasma torch exactly where to go and what to do–from the speed of the cut to the direction and depth of the torch. And whether you're making one piece or a thousand, each cut will be exactly the same.
Plasma Table: The Backbone

The table is the foundation on which everything else rests.
It serves a couple of key functions. First, it provides a flat, stable surface for your material–crucial because any movement or instability can affect the precision of your cuts. Second, it's designed to handle both the intense heat and sparks generated by your plasma-cutting process.
Also, many tables come with additional features designed to make your life easier. Some have built-in clamping systems to hold your material securely in place. Others have water trays to catch sparks and reduce smoke and fumes. And let's not forget about the slats - the metal bars support your material, which are designed to be easily replaceable when they inevitably wear out.
Designing with Ease: Cutting Software
Now that we've got our hardware CNC components sorted, let's talk software. After all, what good is a top-notch plasma torch and a rock-solid table if you don't have an easy way to design and implement your cuts, right?
In a nutshell, this is your digital design studio. It's where you create all your designs or import them from other sources, and then convert them into a language that your CNC controller can understand. Most cutting software supports a wide range of file types, including DXF, SVG, and even PDFs, so you've got plenty of options.
Note that CNC plasma cutting software isn't just about design. It's also where you set your cutting parameters, like the speed of the cut, the height of the torch, and as well as the type of material you're cutting. Some software even includes built-in nesting features, which can help you get the most out of your material by optimizing the placement of your designs.
Powering It Up With Power Supply
None of this high-tech wizardry would be possible without it–like the fuel pump in a car—it keeps everything running smoothly and efficiently.
This unassuming box is what takes your standard electrical input and transforms it into the high-voltage juice needed to generate that plasma we've been talking about. Also, they are specialized units designed to handle the heavy demands of plasma cutting. They regulate voltage, control current, and even ensure that your machine gets a steady, consistent flow of power.
Arc Starting Console (ASC): Igniting the Process
The spark plug. It's what initiates the plasma arc, the super-heated stream of gas that does all the cutting.
It sends a high-voltage spark through the torch to ignite the plasma gas. Once the arc is started, it steps back and lets the power supply take over, maintaining the arc throughout the cut. You know, it's a bit like lighting a gas stove—once you've got the flame going, you can adjust the heat as needed.
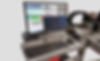
Regulating for Perfection: Gas Console or Flow Control
Why is this important? Well, the type and amount of gas can significantly affect the quality of your cut. Too much gas, and you could end up with a messy, imprecise cut. Too little, and you might not be able to cut through your material at all.
In short, it allows you to dial in the perfect settings for your specific cutting needs.
Transform Your Ideas into Reality with FastCut!
From the powerful plasma torch to the precise CNC controller and your plasma table, each of these CNC machine components plays a crucial role. And the key to leveraging the full potential of these machines lies not just in owning one, but in understanding its capabilities and knowing how to use it effectively.
But of course–this is just the beginning. It's when you see them in action, carving intricate designs and shapes out of a simple sheet of metal, that you truly grasp their power and potential! So, make sure to build your CNC plasma table now!
You’ve got questions? We’ve got answers!
Call Us or Drop Us A Line. We'd love to chat about how our tables can revolutionize your business.