How to Maintain and Troubleshoot Your CNC Plasma Cutter
- russ0377
- Jan 20
- 5 min read
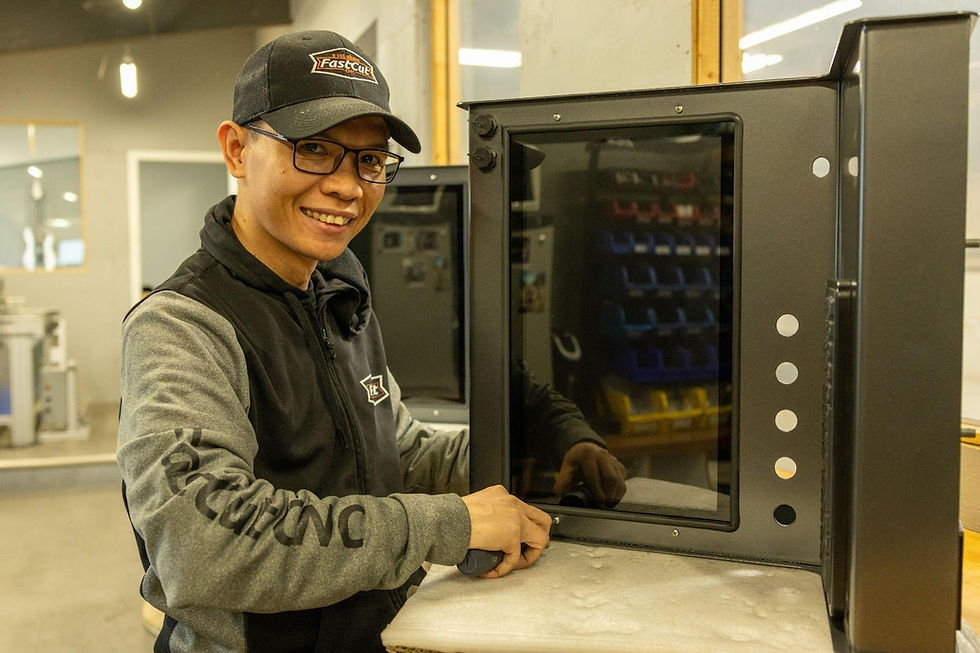
CNC plasma cutters are the powerful and complex heroes of precision metal cutting. Whether you're a weekend warrior building custom projects or running a full-scale fabrication shop, these machines are your ticket to clean cuts and creative possibilities. But like any hardworking machine, they need care to keep performing at their best.
That's why today, here at FastCut CNC, we're sharing our top tips for how to maintain and troubleshoot your CNC plasma cutter so you can extend its life, avoid costly downtime, and achieve flawless cuts every time. From daily maintenance to common issues and how to fix them, we've got you covered!
For Your CNC Plasma Cutter: Keep It Running Like a Champ
Regular maintenance is the foundation of a reliable CNC plasma cutter. Neglect it, and you're asking for trouble. Treat it right, and it’ll serve you for years.
Daily Maintenance
Clean the Torch: After each use, give the torch a good wipe-down. Dust, dirt, and metal shavings love to pile up and mess with your cutting. A clean torch makes for cleaner cuts!
Inspect the Consumables: Take a look at the nozzle, electrode, and swirl ring. And if they’re looking worn out, swap them out before your next cut. Running on worn-out consumables can also lead to shoddy cuts and might even mess up your machine.
Check for Air Leaks: Keep an ear out for any hissing sounds, or spray some soapy water on the connections. Note that air leaks not only mess with your cut quality but can also hike up operating costs.
Weekly Maintenance
Lubricate the Rails and Bearings: To keep your CNC plasma table moving smoothly and precisely, grab those manufacturer-recommended lubricants and give the motion components some love.
Inspect the Plasma Table for Debris: Time to scrape off any slag and tidy up the bed! Yes, a clean plasma table means your material placement and cutting will be spot on.
Check the Air Compressor and Filters: Ensure your air compressor is sending clean, dry air to your cutter. If the air filters look a bit worse for wear, swap them out—they're your first defense against contaminants.
Monthly Maintenance
Check Electrical Connections: Give those wires a look and tighten any that are loose. Keep an eye out for corrosion too. You want reliable power for those smooth cuts!
Calibrate the Machine: Take a moment to check and realign your CNC plasma cutter. Misalignments can cause jagged cuts and waste material, so it's worth the effort.
Update Your Software: Make sure your software is up-to-date, too. Staying current helps with compatibility and boosts efficiency.

Troubleshooting Common CNC Plasma Cutter Issues
Even with a solid maintenance routine, issues can arise.
Torch Misalignment
Ever notice those pesky inconsistent cuts or find yourself wasting material? Your torch might be a little out of whack. But fear not, here's what you can do:
First, take a look and make sure the torch is lined up nicely with your material and table.
Feel around for any mounts or brackets that might be a bit loose and give them a good tightening.
Then, before jumping into your next project, run a quick test cut to be sure everything is in perfect alignment.
Power Fluctuations
Power glitches can throw a wrench in your cutting groove, right? They can even mess up your machine if you're not careful. Here's how to keep things steady:
Plug into a surge protector to keep your power supply stable and your cuts clean.
Double-check that your machine is properly grounded. You don't want any electrical surprises!
Now, if the power ups and downs persist, peek at your power source for consistency. An upgrade might be your best friend here.
Software Errors
Ah, the brains of the operation! Sometimes software can be a real headache, can't it? Here’s how to smooth out those glitches:
Give your CNC plasma cutter software a quick restart. It's amazing what a simple reboot can do for minor glitches.
Make sure your software is on speaking terms with your machine’s firmware—compatibility is key!
Still having trouble? Don't hesitate to reach out to your software provider for some friendly troubleshooting support.
CNC Plasma Table Calibration: The Key to Precision Cutting
You invested in a CNC plasma machine because you know the value of accuracy, right? Well, guess what? Regular calibration is your ticket to ensuring every cut is as sharp as your eye for detail.
Why Calibration is Your Best Friend
Imagine this: your machine is a bit off-kilter, and suddenly, you're wasting materials and time—ouch! But don't worry, because proper calibration is here to save the day. It boosts efficiency, saves you some serious cash, and keeps your projects looking like a pro did them (because, well, you did!).
How to Calibrate Your CNC Plasma Table
Level the Table: First things first, make sure your plasma table is level to prevent those annoying uneven cuts. A spirit level is your best friend here.
Adjust the Gantry: Take a look at the gantry and see if it’s in line with the table rails. It should glide smoothly and evenly.
Square the Torch: Check that the torch is standing straight up. If it’s not, adjust it so you get those nice, clean cuts.
Run a Test Cut: Finally, try a test cut on some scrap material to see if everything's lined up and accurate.
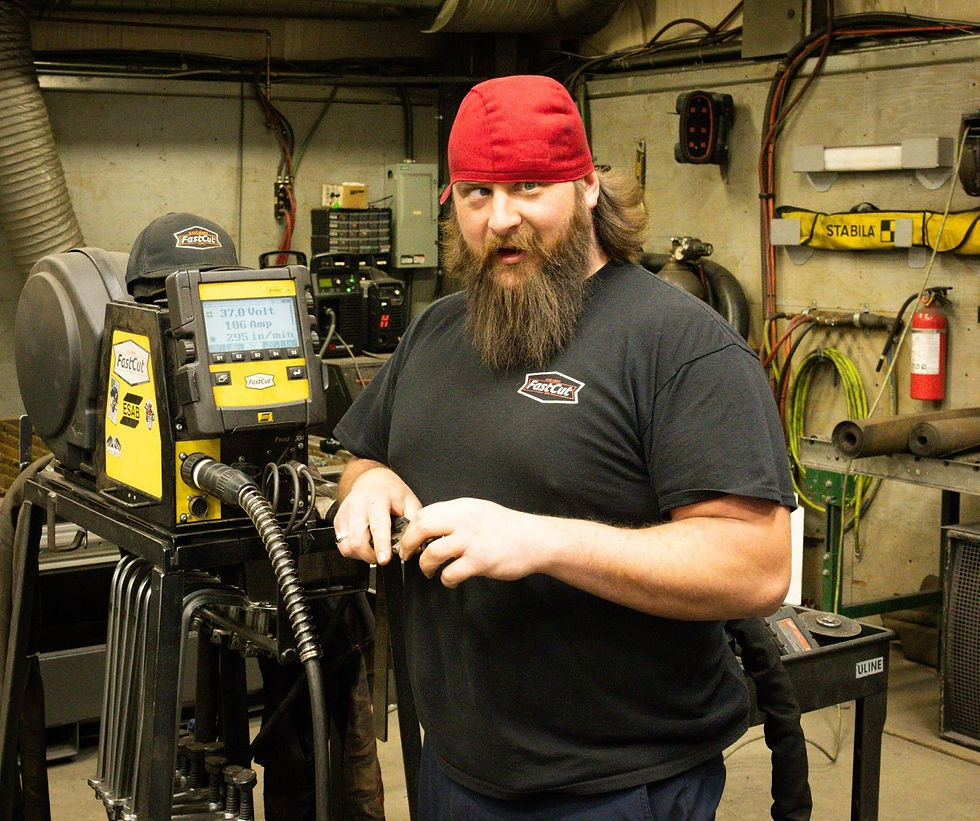
Pro Tips for Keeping Your CNC Plasma Cutter in Top Shape
Go for Quality Consumables
Sure, grabbing cheap consumables might seem like a good deal at first, but they tend to wear out way faster and could even harm your machine over time. If you want your CNC plasma cutter to perform at its best and last longer, it's worth investing in top-notch, manufacturer-recommended parts.
Not only will you see better results, but these parts also boost your equipment’s efficiency and durability.
Train Your Team Well
Now if you've got multiple people using the cutter, it’s super important to make sure everyone’s on the same page. Regular training sessions are key to getting everyone familiar with the maintenance routine, safety protocols, and troubleshooting.
A well-informed team can spot potential issues early on and keep the cutter running smoothly.
Document Everything
Keeping detailed records is super helpful. Make sure to have a maintenance log where you jot down routine checks, part swaps, and any issues or fixes you run into. This documentation can really come in handy when you're trying to figure out future problems, giving you a reference that can even speed up troubleshooting and repairs.
Don’t Overlook Ventilation
Proper ventilation is often something folks forget about when using a CNC plasma cutter. Having good airflow not only extends your equipment's life by preventing overheating and keeping dust and debris at bay, but it also makes a big difference in operator safety. Plus, it also cuts down on exposure to potentially harmful fumes during the cutting process, creating a safer and healthier workspace.
Your Next Step: Keep Your Plasma Cutter Performing Like New With The Best CNC Plasma Table
A well-maintained CNC plasma cutter is more than just a tool—it’s your partner in creating precision metalwork. Stick to a regular maintenance routine, address issues promptly, and recalibrate frequently to keep it running smoothly.
And if you're ready to upgrade or need expert advice, contact FastCut CNC today.
Whether you’re shopping for the best CNC plasma table or need tips on keeping your current machine in top shape, we’ve got you covered!
Commentaires